Technology
Molding Processes
1.Cold Press Cutting Process:
We apply adhesive to the surface materials (fiberglass, carbon fiber, Kevlar, etc.) using machinery, then vacuum press them onto the core materials (PP honeycomb, aramid honeycomb, etc.) to achieve a tight bond. A CNC machine then cuts this bonded panel into your desired paddle shape. UV cured printing applies vibrant graphics to the surface, which is then treated to meet USAPA friction standards (CFS, CAS, sandblasting, PTFE, etc.). Finally, edge guards, handles, and other components are assembled.
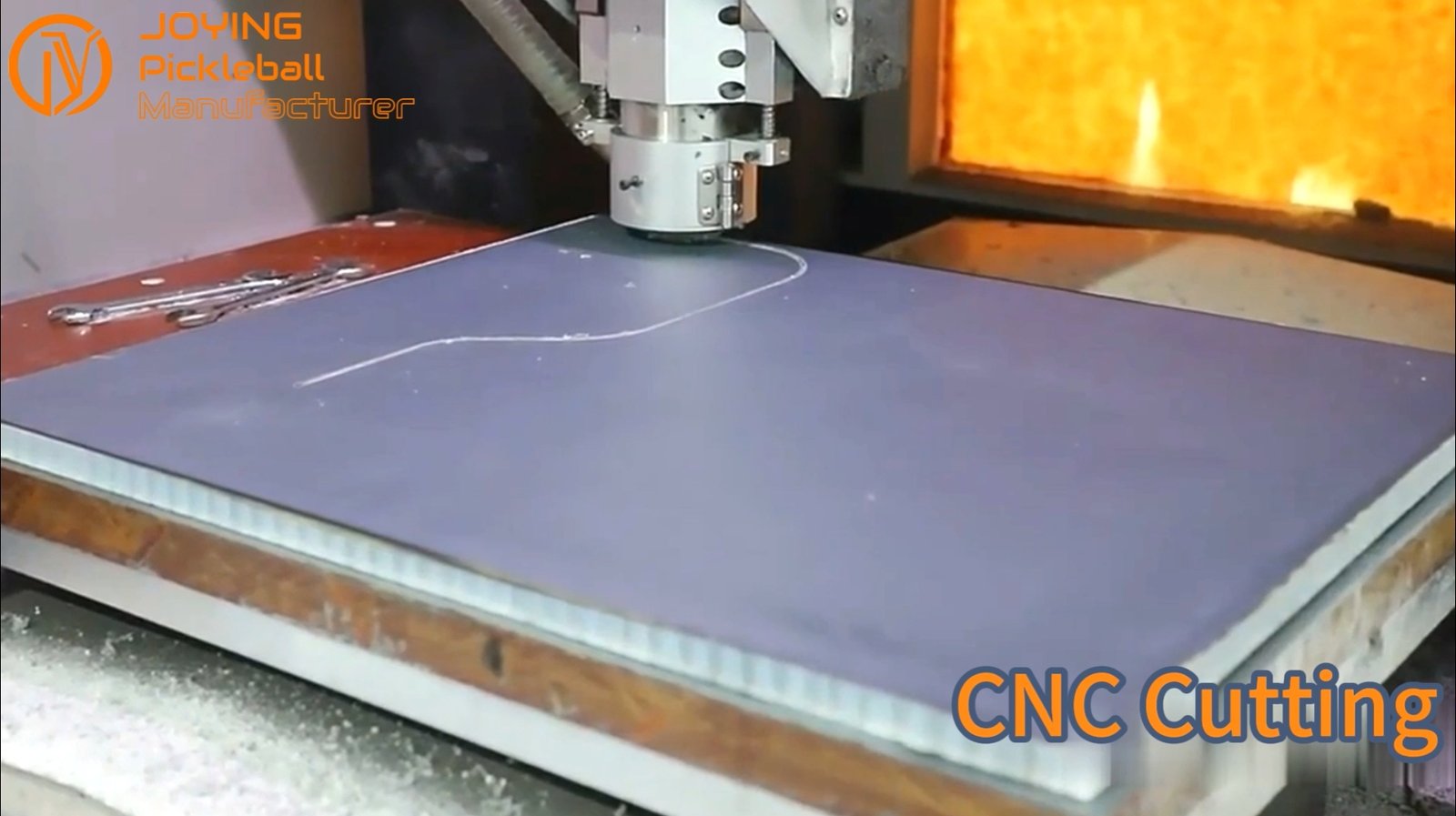
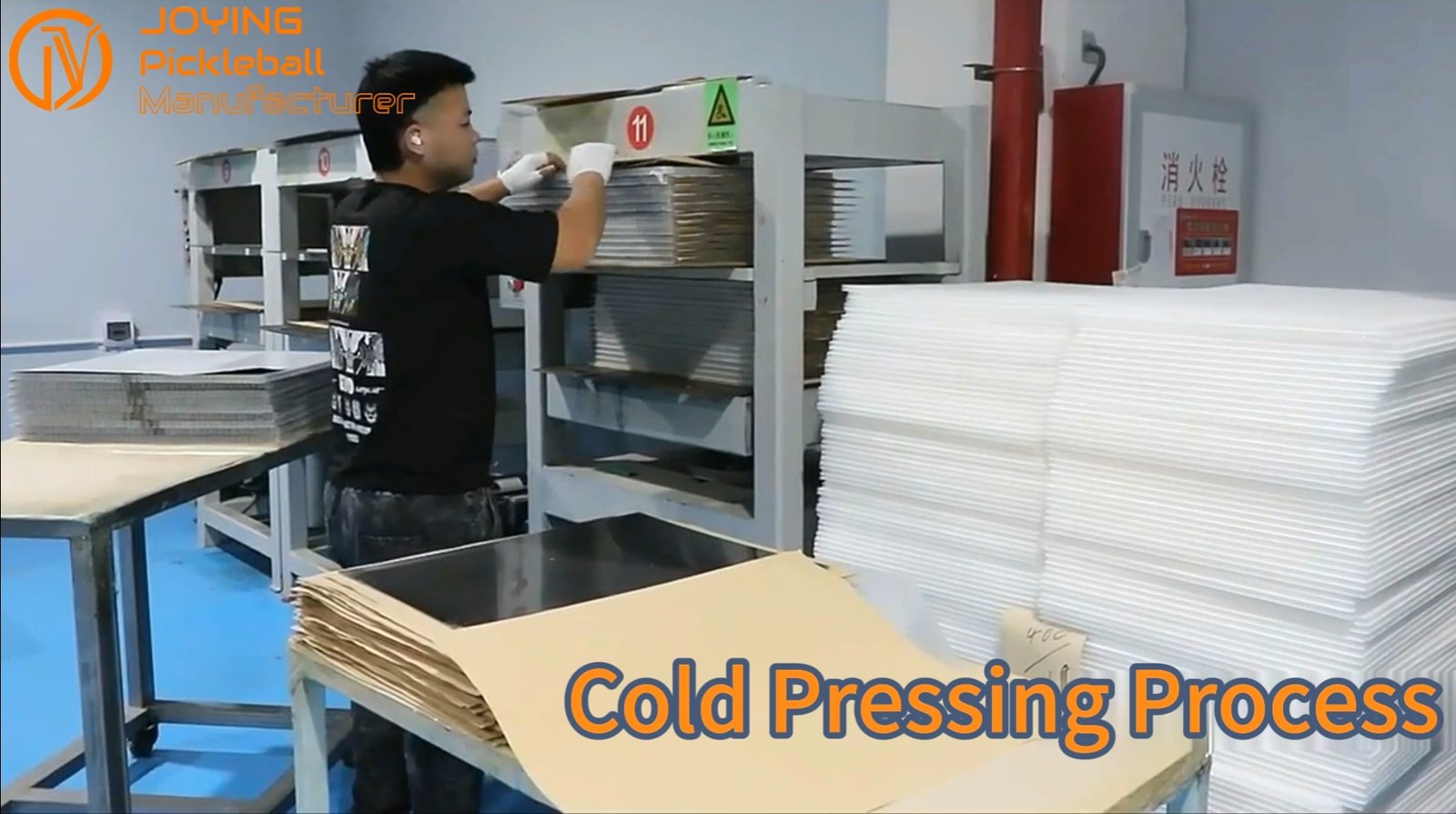
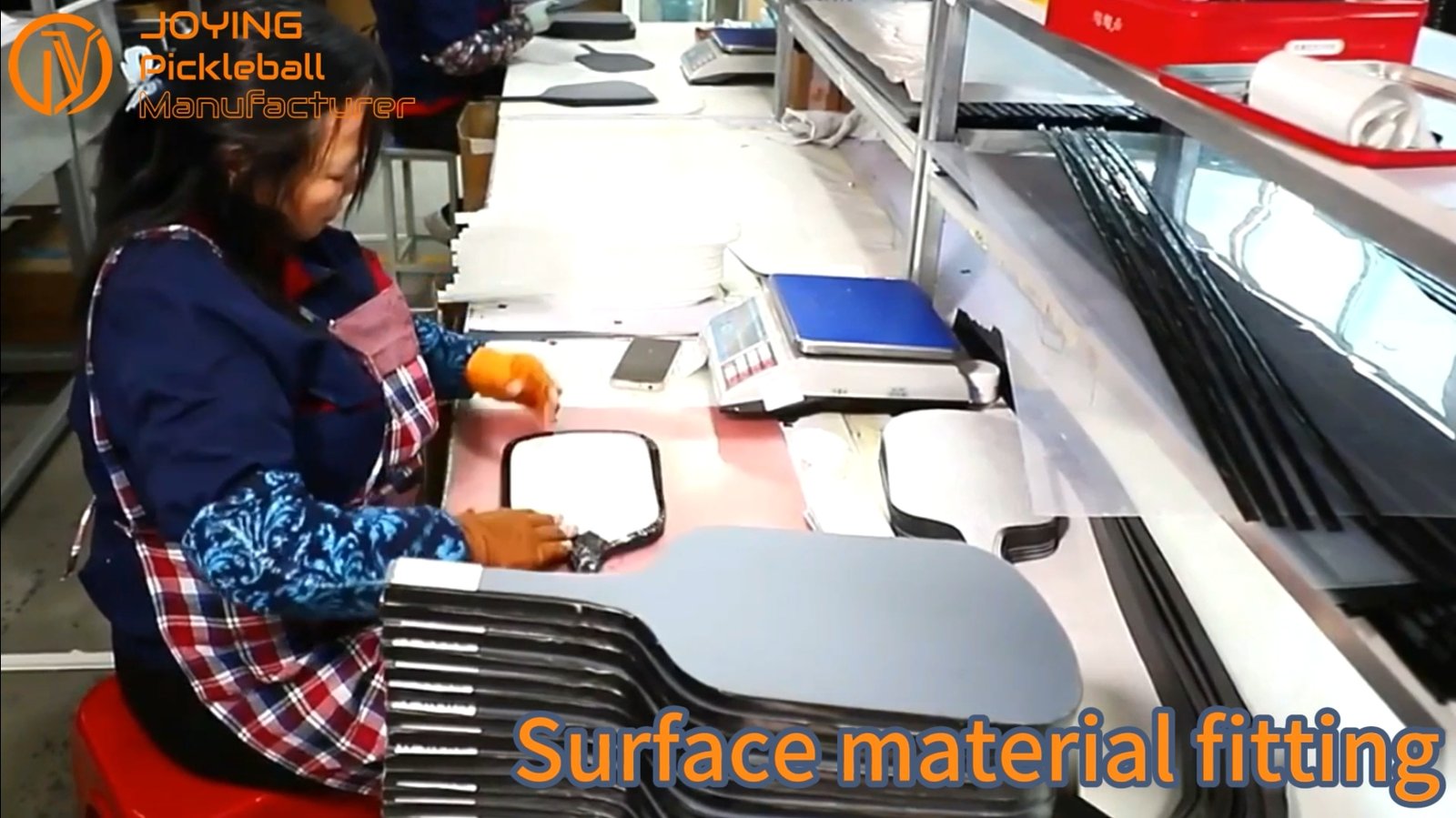
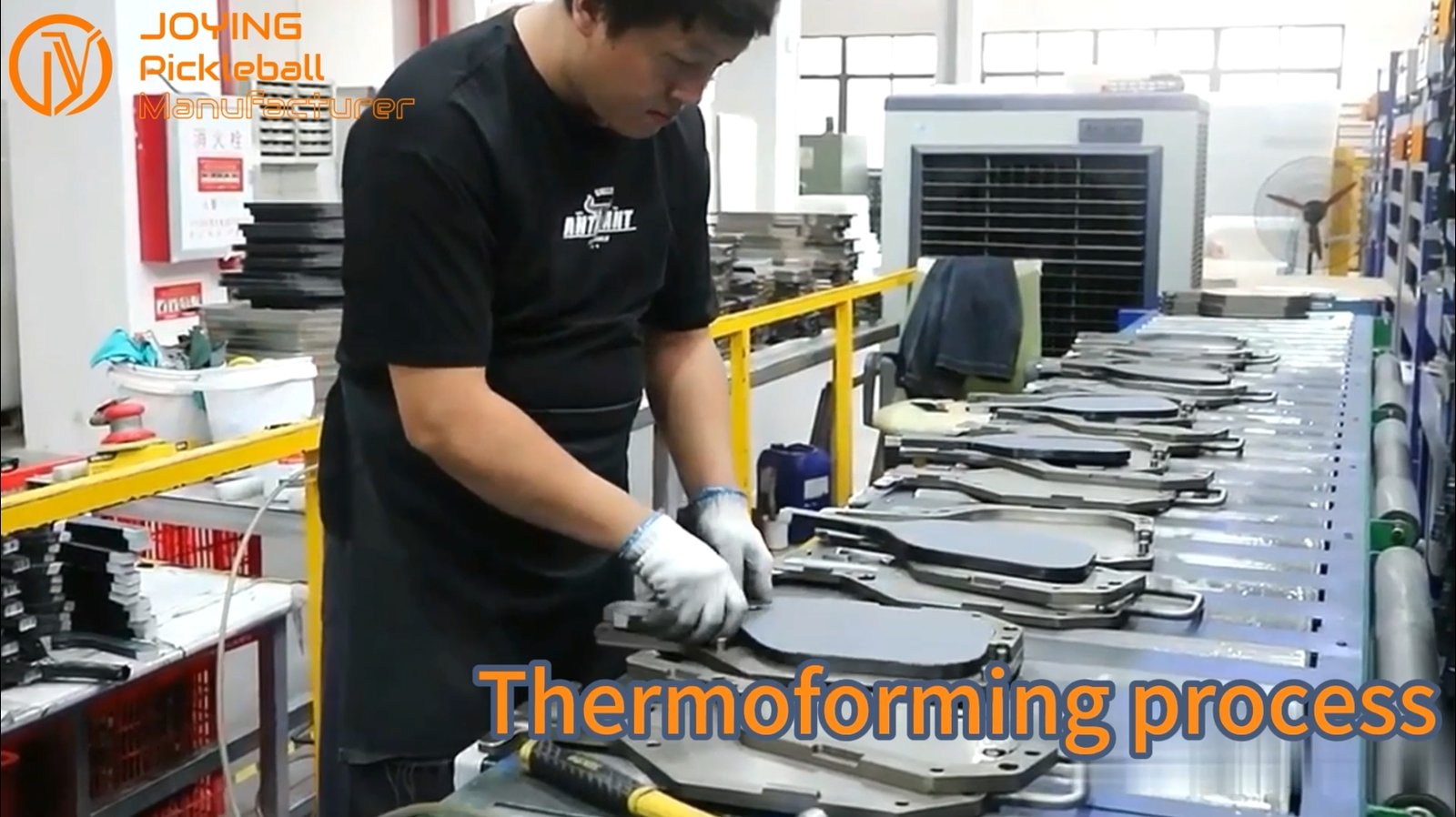
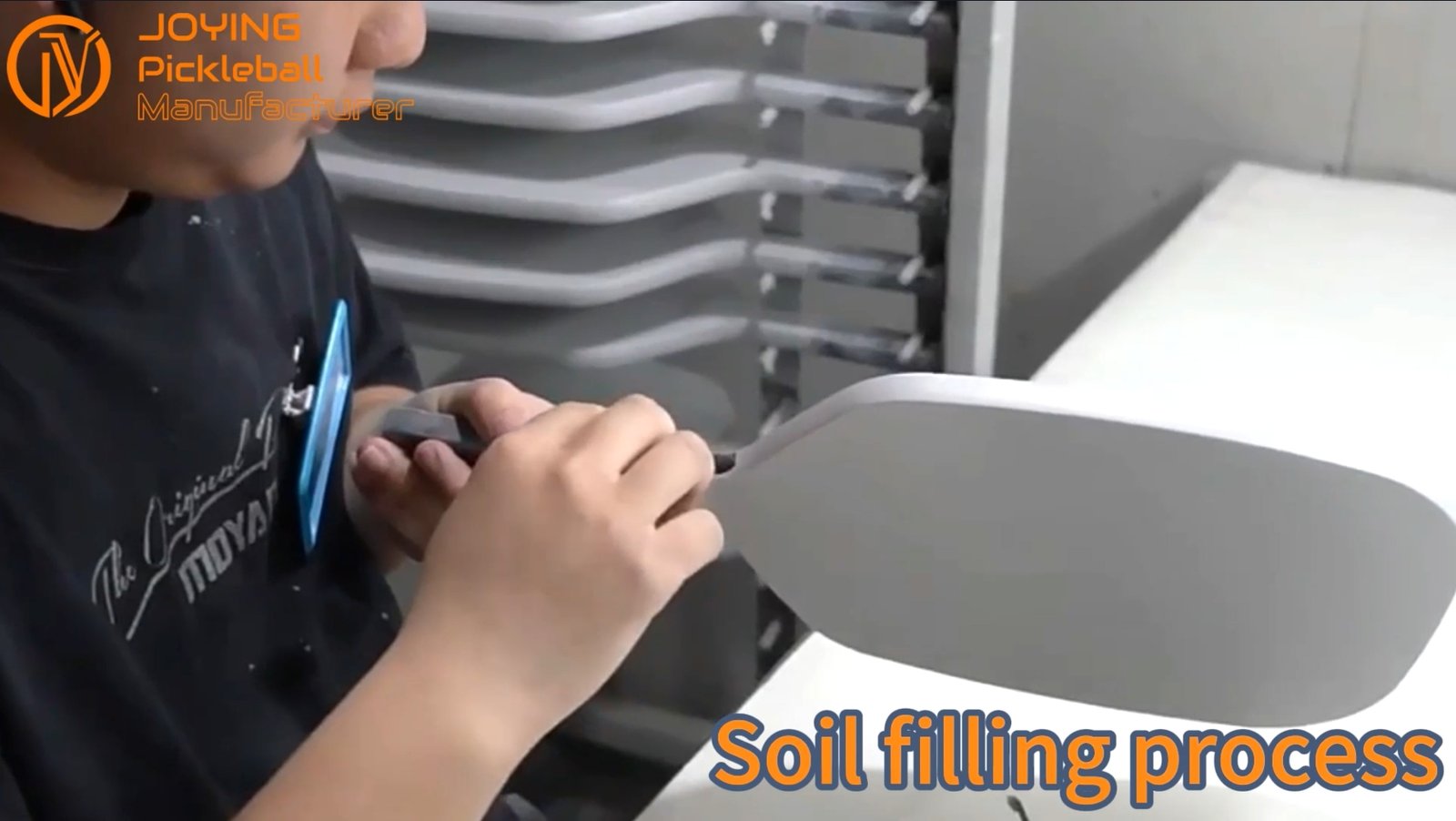

2.Thermoforming Process:
Quality surface materials (fiberglass, carbon fiber, Kevlar) are laid into a heated mold cavity with resin. Pre-cut core materials (PP honeycomb, aramid honeycomb) are placed inside, and the mold is closed and transferred to a high heat/pressure hot molding machine. Simultaneously, foam is injected into the edges to increase molded edge integrity. After cooling, the rough paddle is refined by sanding/patching processes. The surface is treated to USAPA friction standards, printed with UV graphics, and components like edge guards/handles are assembled.
Surface Materials
The surface material is a critical component that largely determines the performance characteristics of a pickleball paddle. The most commonly used materials include fiberglass, carbon fiber, and Kevlar, each offering unique properties:
Fiberglass composite materials offer a well-balanced combination of strength, toughness, corrosion resistance, and relatively low cost. The interwoven glass fibers provide good stiffness and durability, while the polymer resin matrix binds the fibers together. Fiberglass paddles tend to have a solid feel and can produce consistent power and control.
Carbon fiber is renowned for its exceptional strength-to-weight ratio, making it an ideal choice for lightweight, high-performance paddles. The tightly woven carbon fibers, combined with an epoxy resin matrix, result in paddles that are incredibly strong yet lightweight. In addition to their low mass, carbon fiber paddles offer excellent stiffness, toughness, and fatigue resistance, allowing for precise shot-making and extended product life.
Kevlar Fibers are prized for their incredibly high tensile strength, stiffness, and heat resistance. Kevlar composite paddles can withstand substantial impacts and resist deformation, even in hot or humid conditions. The unique properties of Kevlar also contribute to excellent vibration dampening, reducing strain on the arm during play. While more expensive, Kevlar paddles are praised for their uncompromising durability and performance across a wide range of environments.


Surface Textured Technology
1.Micro Sandblasting:
Mixing ultra-fine silica particles into paint, which is sprayed onto the paddle face, creates an evenly distributed surface texture that enhances spin.
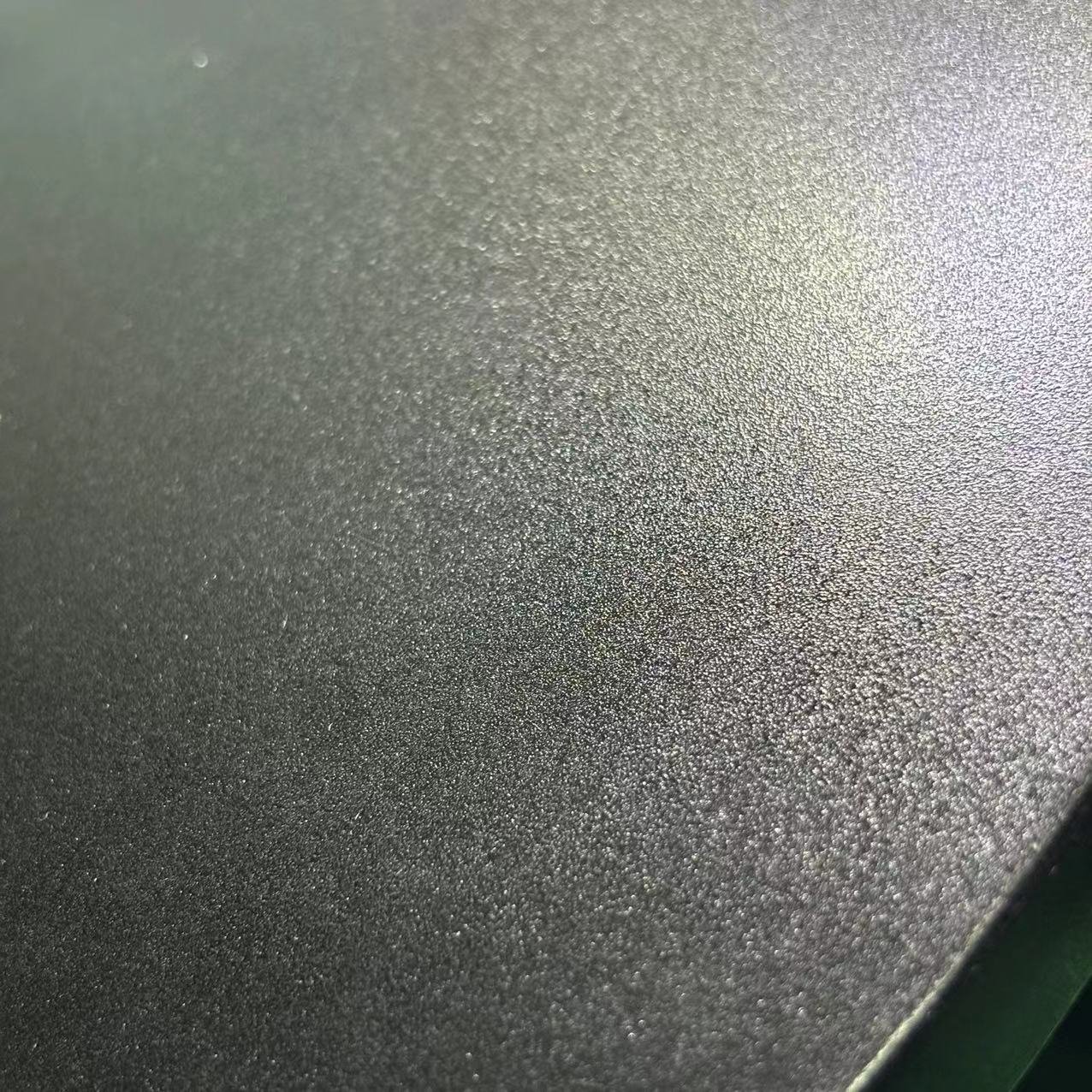

2.Raw Carbon Face
An extra layer of fine woven carbon fiber fabric is applied to the face and sanded to expose the textured weave, increasing friction and spin.
3. 3D Textured Surface:
The three-dimensional texture is transferred to the paddle surface through water transfer printing technology, and then the surface is sprayed with wear-resistant varnish to give the surface a raised line texture to increase surface friction and rotation.

Paddle Edge Technology
1. Edge Guard:
Wrap the edge of the paddle with an Edge Guard made of plastic so that the edge of the paddle will remain intact even if it receives a bump, which can protect the edge of the paddle well.
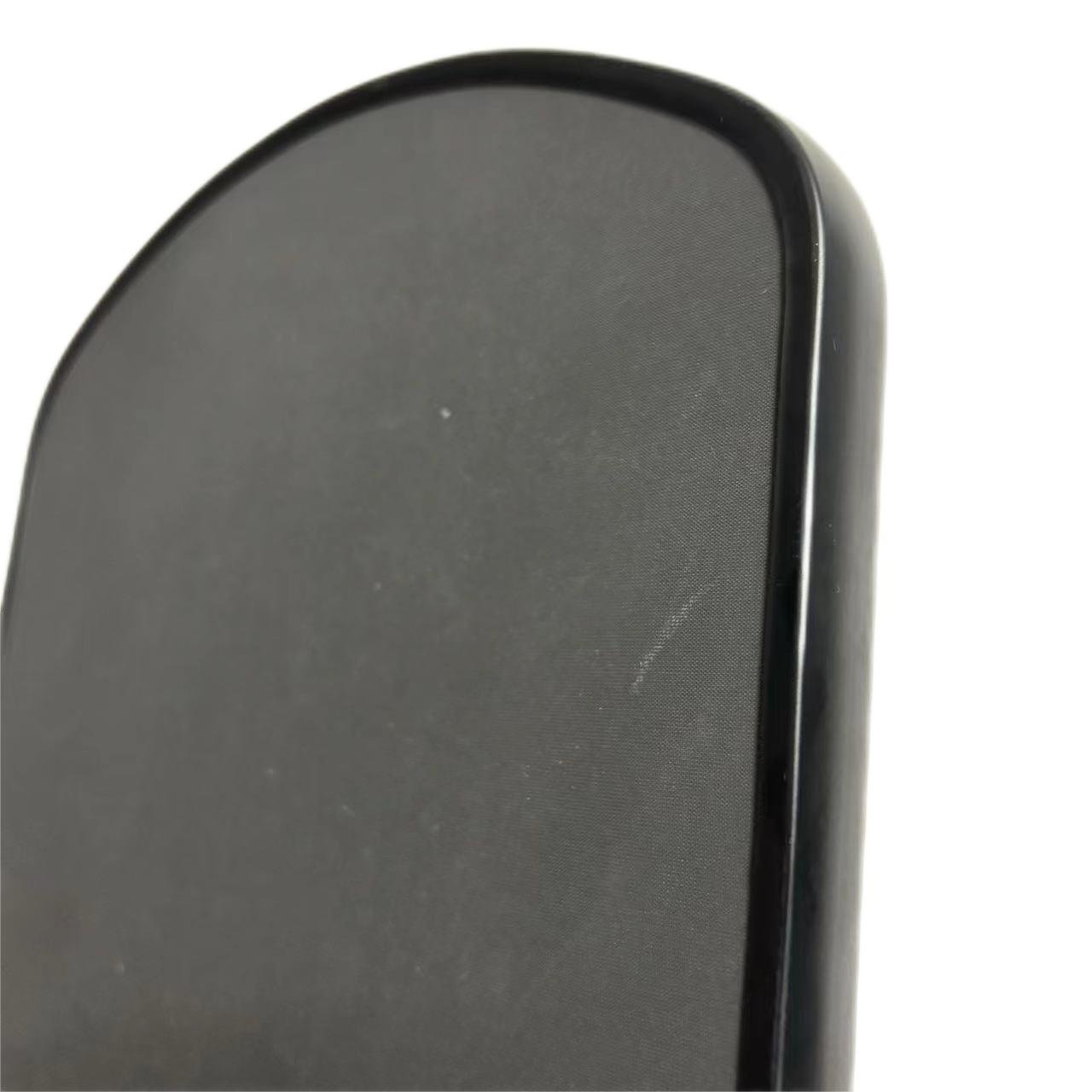
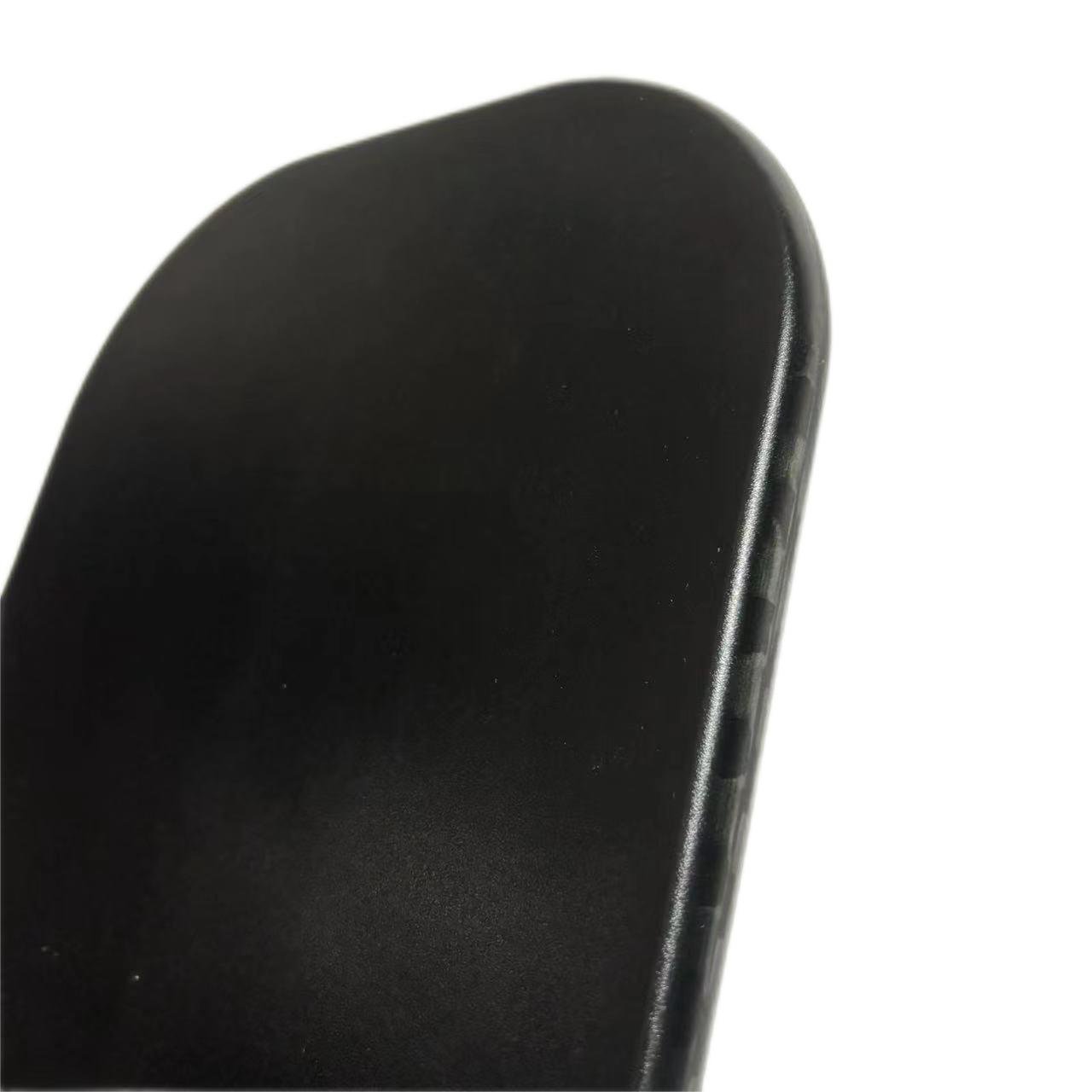
2. Edgeless Process
The edgeless process uses a thermoforming process to seamlessly fuse the edge and surface. The advantage is that it reduces the weight of the edge guard, which reduces the swing weight and makes the paddle easier to control. Due to process limitations, the edgeless process cannot be combined with the Raw carbon face.
3. Edge Blending Process
The edge fusion process is the latest technology. It fuses an additional layer of thinner coating on the edge. It combines the lightweight of the edgeless process and is compatible with the raw carbon face process. It is the process used by top products on the market.

Grip Technology
1. Wood Block & Foam Block Handle
Cut wooden blocks or foam blocks are pasted on both sides of the handle to give the handle a certain shock-absorbing function. This is the handle used by most paddles on the market.
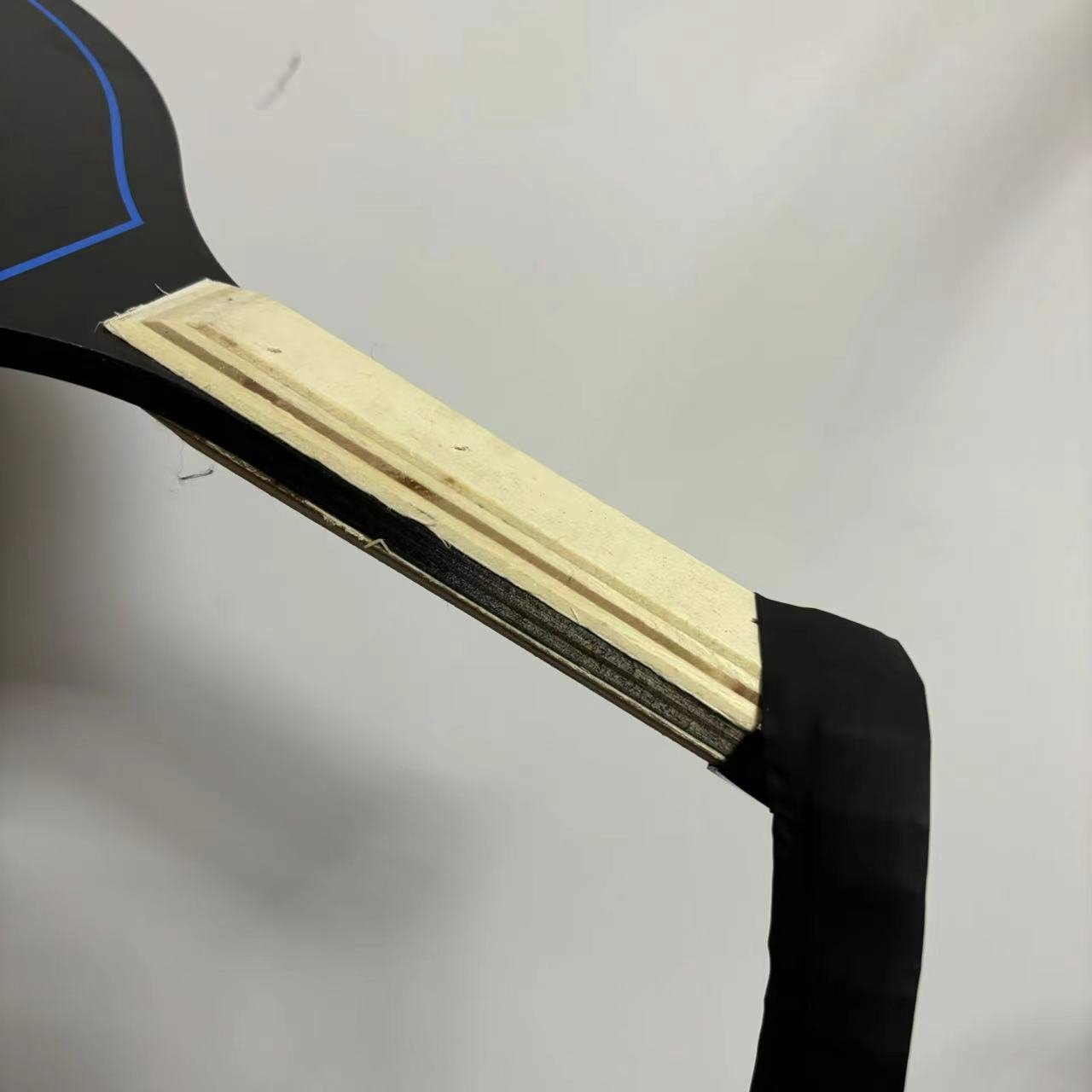
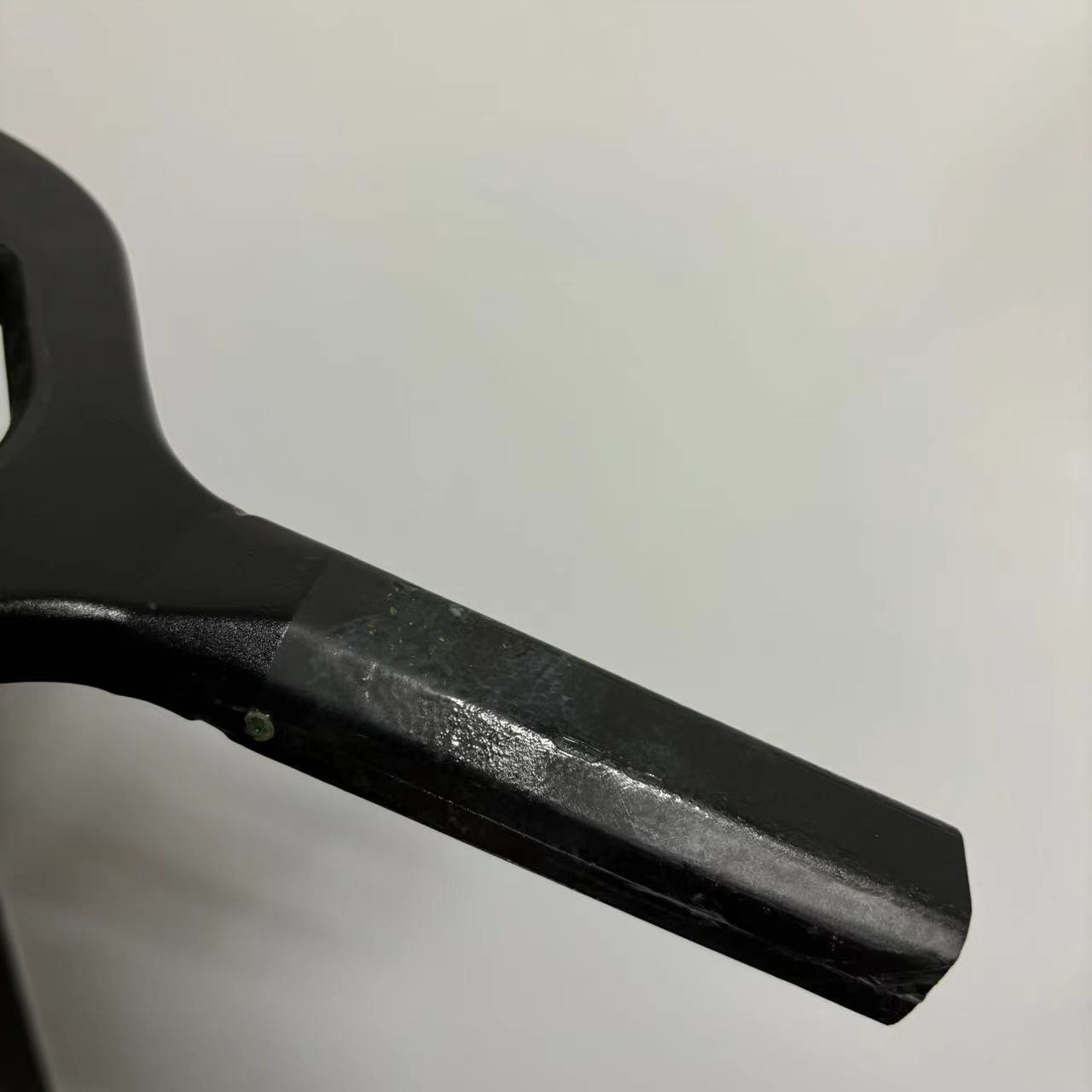
2. Carbon Fiber Integrated Handle
The handle position of the thermoforming mold is designed into an octagonal shape, and the handle part is integrally formed through the thermoforming process, making the handle part stronger and having better power conduction, but the shock absorption function will be slightly weaker.
3. Integrated Foam Handle
The initial handle is placed into a customized foam mold, and the foam is injected to form an octagonal handle shape, which has good shock absorption properties and excellent force conduction, and the circumference of the grip can be customized according to different sizes.
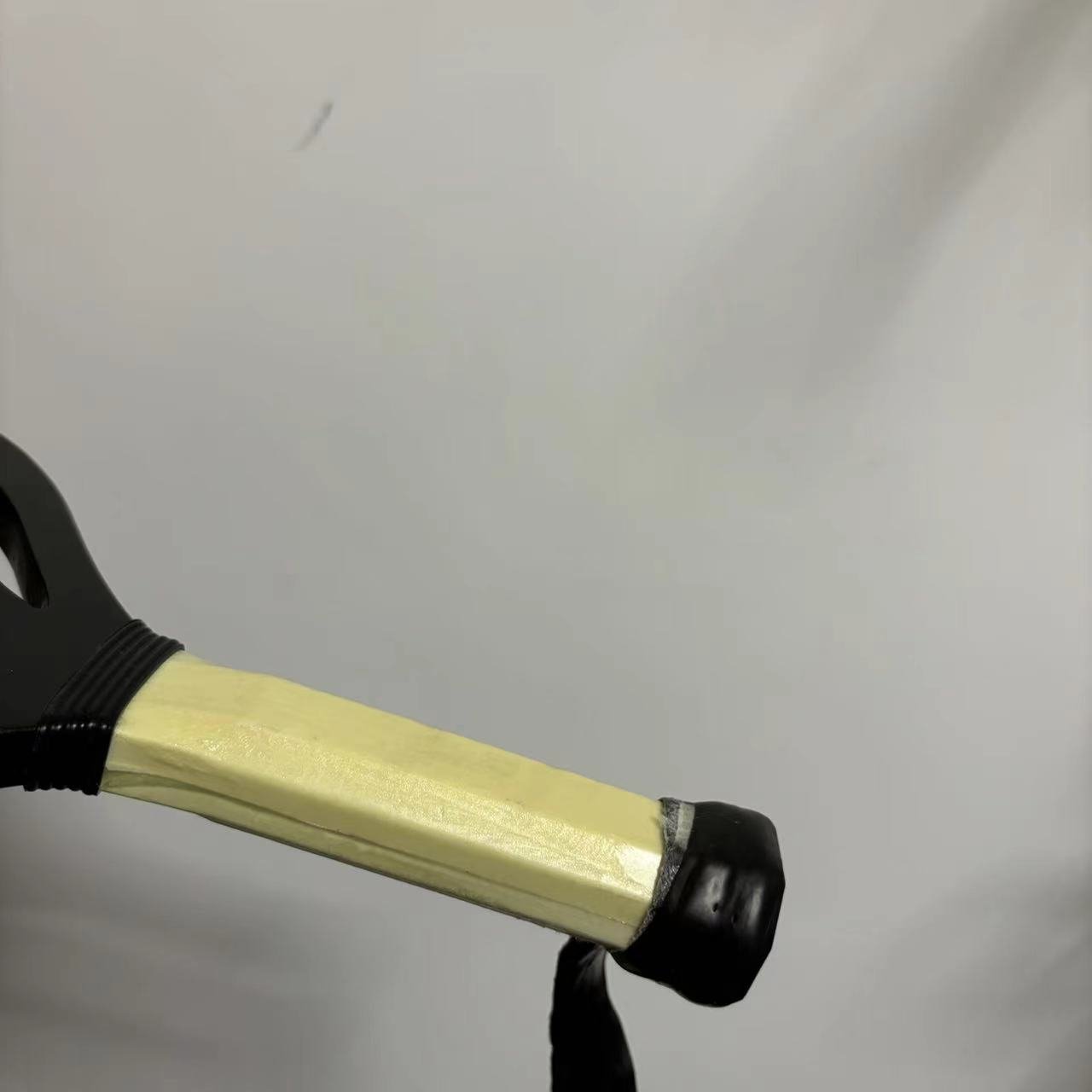